Site Assets
Site assets refer to physical resources or components that are specific to a particular location or site. These assets are typically associated with a specific facility, property, or infrastructure, and play a crucial role in supporting operations, functionality, and services at that specific site.
Site assets can vary depending on the context but generally include tangible items and infrastructure that are essential for the site’s operation and functionality. An example of a site asset is a factory floor.
Factory floor
As a site asset, the factory floor contributes to the functionality and productivity of the manufacturing site. It is designed to accommodate specific production needs, workflows, and equipment requirements. The factory floor may include features such as designated work areas, production lines, conveyor systems, storage areas for raw materials or finished goods, safety markings, and access points for employees and machinery.
The factory floor is crucial for ensuring smooth operations, effective utilization of resources, and efficient production processes. It is where the actual manufacturing activities occur and where site-specific equipment, machinery, and workers come together to produce goods. Optimizing the layout and organization of the factory floor can have a significant impact on productivity, quality control, and overall operational performance within the manufacturing site.
Distributed Industrial Asset sector
The site assets within a Distributed Industrial Asset sector are characterized by their geographic distribution across different physical locations. They are interconnected through communication networks, enabling data exchange, monitoring, and control across the distributed network. These assets may also be equipped with sensors and connected devices for real-time data collection and analysis.
The rise of Distributed Industrial Assets, characterized by geographically dispersed physical resources and advanced connectivity, has transformed manufacturing and industrial processes.
Within this landscape, digital twins have emerged as a powerful tool, providing virtual representations and real-time simulations of physical assets and processes. We will explore further the pivotal role digital twins play in the realm of Distributed Industrial Assets, focusing on their significance on the factory floor.
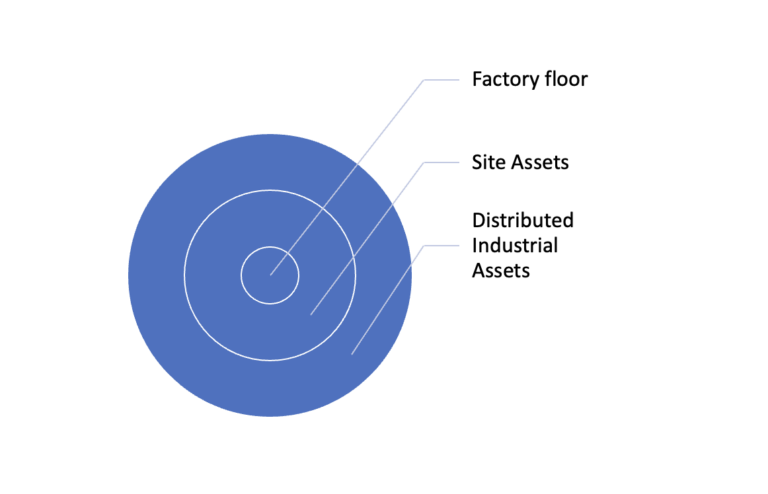
Digital twins in the Distributed Industrial Asset sector
- Asset Performance Monitoring:
Digital twins enable real-time monitoring of machinery, equipment, and production lines across multiple factory sites. By integrating sensor data and relevant inputs, digital twins capture and analyze asset performance metrics such as temperature, vibration, energy consumption, and production output. This continuous monitoring helps identify anomalies, predict potential failures, and optimize asset performance, ensuring maximum efficiency and uptime.
- Predictive Maintenance:
Digital twins facilitate proactive maintenance strategies for distributed industrial assets. By analyzing data from sensors and historical records, digital twins detect patterns, identify maintenance requirements, and predict asset failures or degradation. This data-driven approach minimizes unplanned downtime, optimizes maintenance schedules, and extends the lifespan of assets, resulting in significant cost savings.
- Simulation and Optimization:
Digital twins provide a digital replica of distributed industrial assets and processes, enabling simulation and optimization without disrupting the actual production environment. Operators can test and evaluate different scenarios, optimize production workflows, and adjust resource allocation. This empowers them to identify process improvements, enhance efficiency, and maximize resource utilization, ultimately driving operational excellence.
- Remote Monitoring and Control:
Through IoT integration and connectivity, digital twins enable remote monitoring and control of distributed industrial assets. Operators and engineers can remotely access and monitor assets’ status, parameters, and performance from different locations. Real-time data analysis empowers them to make informed decisions and adjust operational settings as needed, ensuring seamless control and coordination across the distributed network.
- Training and Simulation:
Digital twins serve as invaluable training and simulation platforms for operators and maintenance personnel. They create a safe and controlled environment for acquiring skills, practicing procedures, and improving expertise. Operators can simulate realistic scenarios, test strategies, and enhance their understanding of asset operation and maintenance, fostering a culture of continuous learning and development.
- Data Analytics and Process Optimization:
Digital twins harness the power of data analytics to optimize processes in distributed industrial asset environments. By collecting and analyzing data from various sources, including sensors, equipment logs, and production systems, digital twins unveil insights into process inefficiencies, bottlenecks, and opportunities for improvement. This data-driven approach facilitates informed decision-making, continuous improvement efforts, and the pursuit of operational excellence.
Digital twins ensure a factory floor safety
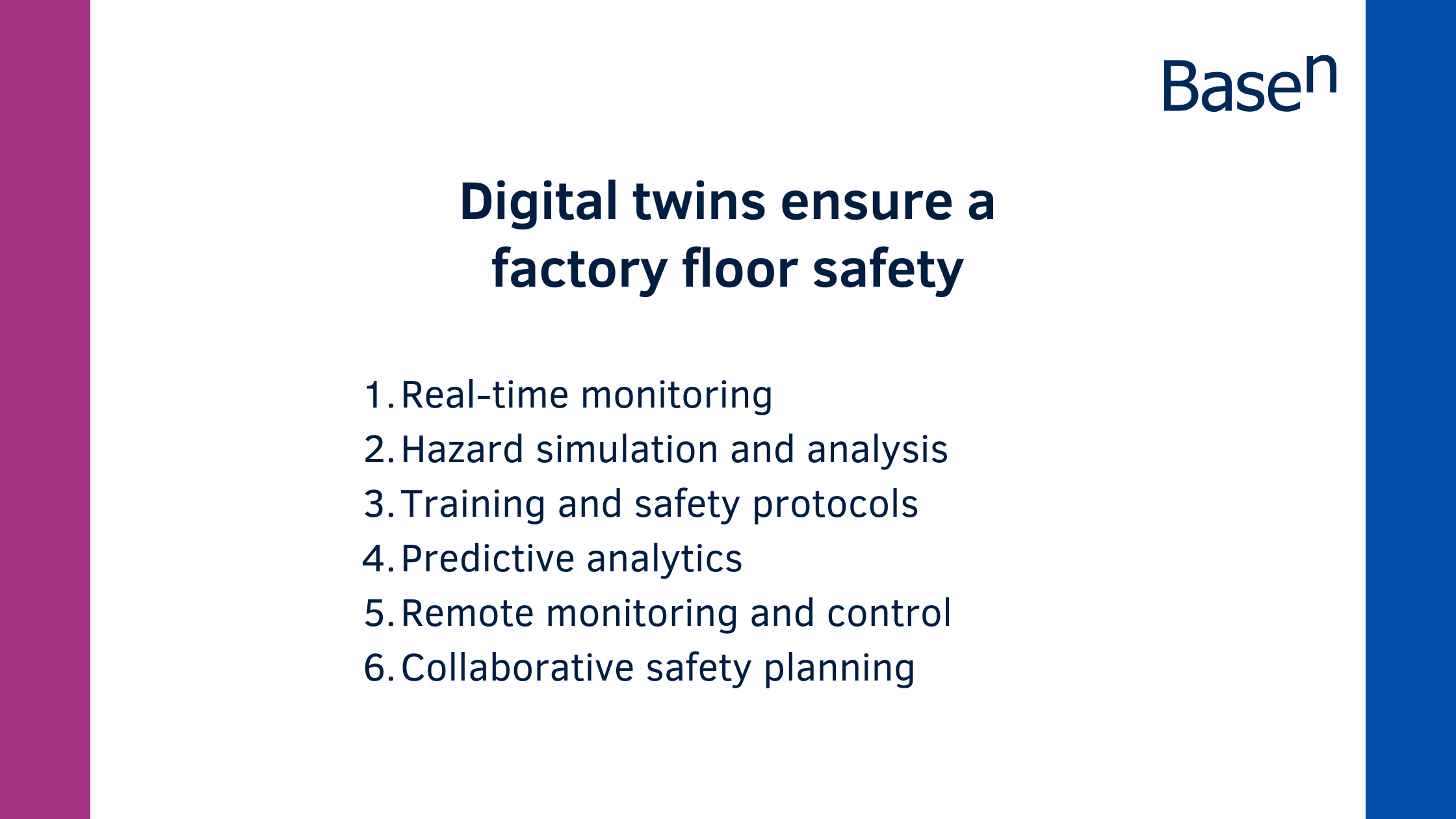
- Digital twins enable real-time monitoring of the factory floor and its assets. By integrating sensor data from various sources, such as cameras, motion sensors, temperature sensors, and gas detectors, digital twins can continuously monitor the working environment for potential safety hazards. Any abnormal conditions or safety breaches can be detected promptly, allowing for immediate action to mitigate risks.
- Digital twins allow for the full situational awareness and analysis of potential safety hazards on the factory floor. By enabling a digital incarnation of the physical environment, including machinery, equipment, and worker interactions, digital twins can simulate different scenarios and identify potential safety risks. This helps in understanding how different factors contribute to safety hazards and enables proactive measures to be taken to prevent accidents.
- Digital twins serve as training platforms for safety protocols and emergency response procedures. Workers and employees can practice safety drills and simulate emergencies within the virtual environment of the digital twin. This helps in familiarizing them with the correct safety procedures, improving their response times, and enhancing overall safety awareness.
- Digital twins can leverage predictive analytics to anticipate safety risks and prevent accidents. By analyzing historical data, sensor inputs, and real-time information, digital twins can identify patterns or anomalies that could indicate potential safety hazards.
- Digital twins facilitate remote monitoring and control of the factory floor, enabling safety personnel to oversee operations from a centralized location. Safety personnel can remotely monitor the factory floor, identify unsafe conditions, and intervene if necessary, ensuring immediate response to safety concerns.
- Digital twins enable collaborative safety planning and communication among different stakeholders involved in factory floor safety. Safety protocols, risk assessments, and preventive measures can be shared and discussed within the digital twin environment. This promotes better coordination and alignment between safety teams, management, and workers, leading to a safer working environment.
As Distributed Industrial Assets continue to reshape industrial landscapes, digital twins have emerged as a game-changer on the factory floor. Digital twins enhance factory floor safety by providing real-time monitoring, hazard simulation, predictive analytics, training opportunities, remote control capabilities, and collaborative safety planning. By leveraging these capabilities, organizations can proactively identify and address safety risks, minimize accidents, and ensure a safer working environment for employees.
With improved efficiency, reduced downtime, and enhanced productivity, digital twins are revolutionizing the way industrial processes operate, paving the way for a smarter and more agile future. Embrace the power of digital twins and embark on a transformative journey toward industrial excellence.